TPO vs. PVC Roofs: The Complete Guide to Single-Ply Roofing for South Bay Warehouses
Why This Decision Matters in the South Bay
The South Bay’s warehouse corridor—from Redondo Beach to Carson—faces:
High solar load: 280+ sunny days a year push roof-surface temp past 160°F.
Salt-laden marine layer: Accelerates plasticizer loss in older membranes.
Industrial contaminants: jet fuel residue, restaurant grease vents, and chemical drips at loading docks.
Rising utility rates: SCE’s tier-2 kWh price climbed 34% in five years.
Your roof isn’t just waterproof; it’s an energy-saving, chemical-blocking, solar-ready asset. Two single-ply contenders dominate spec sheets:
Membrane | Full name | Core polymer | Typical thickness | South Bay market share* |
TPO | Thermoplastic Polyolefin | Polypropylene + EP (rubber) | 45-, 60-, 80-mil | ~55 % |
PVC | Polyvinyl Chloride | PVC + plasticizers | 50-, 60-, 80-mil | ~35% |
*Based on 2024 permit data, Torrance & LA County.
Both use heat-welded seams, sheet rolls up to 12 ft wide, and adhere over polyiso insulation boards. But performance diverges on four mission-critical fronts.
1. Energy Efficiency: TPO’s Reflective Edge
1.1 Solar Reflectivity Numbers
Product example | Initial Solar Reflectance (ASTM C1549) | Aged 3-yr | SRI | Cool-Roof rebate eligible? |
TPO 60-mil white (Carlisle Sure-Weld) | 0.79 | 0.70 | 90-95 | Yes (Title 24) |
PVC 60-mil white (Sika Sarnafil) | 0.74 | 0.68 | 95 | Yes |
Baseline dark BUR | 0.06 | 0.05 | 2 | No |
Takeaway: TPO’s polyolefin surface stays slightly brighter after three marine-layer seasons, shaving 2-3 °F more off roof-deck temps.
1.2 Cooling-Cost Impact in Torrance
See the bar chart for a 200,000 ft² logistics center on Del Amo Blvd. We modeled annual HVAC demand with DOE’s Cool Roof Calculator (Climate Zone 09).
Baseline dark BUR = 100 % cooling index
TPO 60-mil = 82 % (18 % energy savings)
PVC 60-mil = 85 % (15 % savings)
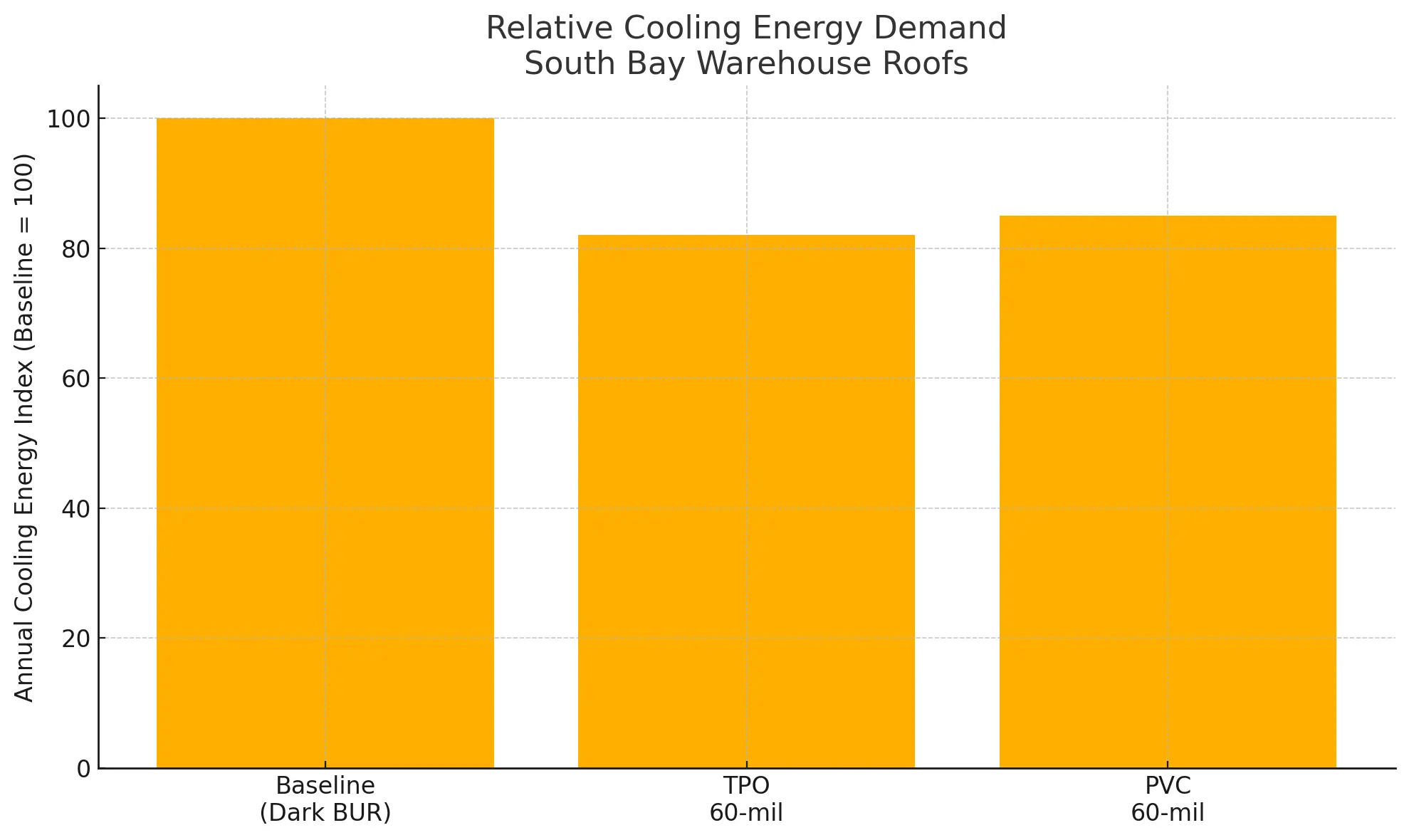
2. Chemical Resistance: PVC’s Proven Shield
Forklift battery acid, restaurant fry-hood grease, and aviation fuels splatter across South Bay warehouse roofs daily. Chemical splashdown eats polyolefins quicker than chlorinated PVC.
Contaminant | PVC lab rating (ASTM D543) | TPO lab rating | Field note |
Jet fuel (Jet-A) | Excellent | Fair | Seen at Hawthorne aerospace suppliers |
Animal/vegetable grease | Excellent* | Poor | Torrance food-distribution hubs |
Sulfuric acid (dilute) | Good | Poor | Forklift‐battery charging stations |
*PVC’s plasticizers resist hydrocarbon breakdown; TPO may craze within 5–7 yrs if uncleaned.
3. Solar Compatibility: Mounting Arrays without Voiding Warranty
Factor | TPO | PVC |
Heat buildup under racking | Slightly cooler deck; lowers PV cell temp | Comparable when white; darker PVC heats faster |
Chemical leach from panel frames | No issue | Aluminum leach can soften low-plasticizer PVC* |
Attachment method | Ballast, clamps, or fully-adhered systems | Same, but some PVC OEMs restrict adhesive types |
Installer learning curve | Common | Common |
*Premium KEE-PVC blends (Carlisle FleeceBACK KEE HP) mitigate this risk.
Both membranes weld well around stanchions and resist membrane fluttering under uplift loads. Our principal roof consultants insist on slip-sheets under ballast pavers for either system to prevent abrasion.
4. Maintenance & Life-Cycle Costs
4.1 Longevity & Warranties
Thickness | TPO warranted life | PVC warranted life |
45-mil | 15-yr | 20-yr |
60-mil | 20–25 yr | 25–30 yr |
80-mil | 30 yr | 30–35 yr |
PVC’s plasticizer loss—once its Achilles heel—now slows thanks to KEE modifiers, closing the gap with thick TPO sheets.
4.2 Cost Breakdown- (200,000 ft² South Bay Warehouse)
Line item | TPO 60-mil fully-adhered | PVC 60-mil fully-adhered |
Membrane + accessories | $1.85 / ft² | $1.85/ft² |
Polyiso R-20 insulation | $1.90 | $1.90 |
Labor & attachment | $1.40 | $1.50 |
Tear-off & disposal | $0.55 | $0.55 |
Subtotal | Net installation cost | $6.30 / ft² |
SCE cool-roof rebate | –$0.15 | –$0.15 |
Net install cost | $5.70/ft² | $6.15/ft² |
25-yr maintenance (NPV) | $0.45 | $0.30 |
25-yr life-cycle cost | $6.00 / ft² | $6.45 / ft² |
TPO starts cheaper, but higher chemical-damage repairs can erase that gap in grease-heavy facilities by year 12.
5. Installation Methods & Detailing
Fully adhered systems : Preferred over mechanically attached installations near the coast—fewer fastener penetrations and no membrane fluttering in Santa Ana winds.
Mechanically attached: Fast for large rolls, but risk of uplift and flutter on 30-ft bays.
Ballasted: Rare now; ballast loads exceed older roof-deck designs.
Roof90-mil membrane: Overkill for low-traffic decks—save cap-ex unless chemical attack is extreme.
Our award-winning building-enclosure team uses infrared drones for roof condition assessment and registered roof observers (RRO) for quality assurance on every weld.
6. Code & Insurance Considerations in LA County
Title 24 Cool-Roof rules demand initial SR ≥ 0.70 and aged SR ≥ 0.63 (both membranes meet with white top layer).
UL 790 Class-A fire: Both pass with underlying gypsum coverboard.
FM-4470 uplift: 60-mil sheets over ½-in HD polyiso, 6-in o/c fastener pattern, exceed 1-60 rating.
Insurance claims: Underwriters favor PVC for chemical-processing plants; may cut premiums 2–4 %..
7. Practical Decision Matrix for South Bay Warehouses
Primary need | Best membrane | Why |
Minimize cooling energy (3+ HVAC units) | TPO | Highest reflectivity; lower surface heat |
Frequent chemical/grease exposure | PVC | Superior chemical resistance, welded watertight seams |
Heavy forklift/battery acid splash | PVC | Acid-proof, longer lifespan under spills |
Budget-tight tenant improvement | TPO | Lower install cost, quicker ROI on energy savings |
Solar-array ready (ballasted) | Either | Both weld around stanchions; TPO stays cooler |
30-yr hold-and-own strategy | PVC 80-mil | Longest warranty; proven durability |
Flip in 10 years | TPO 60-mil | Lower cap-ex, still nets green-building points |
8. Expert Tips to Extend Membrane Lifespan
- Use walkway pads at all service doors to stop pallet-jack wheel gouges.
- Schedule semi-annual roof inspection—clears grease traps before they etch TPO.
- Specify ¼-in coverboard under either membrane for hail and foot-traffic resistance; adds 18 ¢/ft², saves thousands in puncture repairs.
- Choose 60-mil minimum; 45-mil lasts under Arizona sun, not Torrance’s salt-fog/UV combo.
- Embed a leak-detection grid (low-voltage ELDS wire) for easier pinpointing beneath solar arrays.
Conclusion & Recommendation
Both TPO and PVC single-ply roofs satisfy Title 24, deliver cool-roof energy savings, and weld into a watertight skin—but they excel under different battlefield conditions:
- Choose TPO roofing (Torrance warehouses) when energy efficiency and lower up-front cost top your list, and chemical splash risk is minimal.
- Opt for PVC roofing if your operation vents grease, fuels, or harsh chemicals—its chemical resistance and longer service life outweigh the extra 60 ¢ per square foot.
Still on the fence? The right answer often hides in roof-deck details, HVAC layouts, and lease-term math.
Next Step: Book a Free Single-Ply Roof Inspection & 25-Year Cost Report
Call +1 (424) 492-2022 or click “Schedule My Assessment.”
We’ll:
- Scan your roof deck with drones and infrared for hidden moisture.
- Produce a side-by-side 25-year cost-of-ownership model (TPO vs. PVC) tailored to your kilowatt rate and chemical exposure.
- Deliver a permit-ready quote—no charge, no obligation.
Author: Jack Gray, RRO, Principal Roof Consultant, Moriarty Corp.
Sources:
Southern California Edison, Schedule GS‑1 Tariff Sheets 2020‑01 vs 2024‑01.
LA County Department of Public Works, Building Permit Records (query on 22 May 2025; 1,012 reroof permits, 2024).
Moriarty Corp. Project File #CR‑23‑0413, Harbor Gateway KEE‑PVC Retrofit, 2023.